When your home inspector notes a deficiency in your chimney or fireplace it is very important to get a qualified fireplace professional or certified chimney sweep to evaluate and make repairs. Fireplaces and chimneys are complex and it takes special training and knowledge to build and maintain them. This discussion will describe the most common types of wood burning fireplaces and point out typical construction details as well as the most common defects that we find.
There are basically two types of masonry fireplaces. A traditional fireplace has a firebox which is at least 20” deep. These are multipurpose fireplaces designed for a variety of tasks. A Rumford has a more narrow firebox (minimum 12”) and is designed more for heating. It is characterized by a rounded throat which many believe draws better than a traditional fireplace. They also tend to reflect more heat back into the room.
Parts of a Fireplace and Chimney
Study the images below which identify some of the major parts of the fireplace.
Typical Construction Details
Walls of a chimney with a clay flue lining should be at least 4” thick.
Unlined chimney walls of 4” brick is a defect.
Although unlined masonry chimneys (minimum thickness 8”0) will operate satisfactory a glazed flue lining is recommended.
As a rule, a single flue should be used for only one heating unit.
Corbelling should not exceed a 1” projection for each course.
Joints in the flue lining should be bedded in mortar or fireclay.
At the top the flue lining should extend at least 4” above the top course or capping of cement mortar at least 2” thick.
When several flues are located in the same construction, it is best to extend them to different heights.
Offsets should be limited to 60 degrees.
The side and back walls of the combustion chamber continue up to the level of the damper. These must be lined with firebrick at least 2” thick set in a special clay mortar that will withstand the heat. Total thickness including the firebrick should be at least 8”.
Cross sectional areas of the throat should not be less than that of the flue. Its length should always equal the width of the fireplace opening. Vertical distance of about 6-8”.
Depth of the smoke shelf should not be less than 4” but can be up to 12” or more depending on the depth of the fireplace.
The purpose of the smoke shelf is to help change the direction of downdrafts. It is usually made as wide as possible and curved to reduce turbulence in the air flow.
The smoke chamber extends from the top of the throat to the bottom of the flue. This space helps keep smoke from being forced back into the room by decreasing the force of downdrafts.
Side walls of the smoke chamber are drawn inward typically one foot for every 18” of rise. All surfaces of the smoke chamber should be plastered smooth with at least a ½” of cement mortar.
In order to develop a draft sufficient to draw smoke a fireplace and chimney should be a minimum of 12’ high. A shorter chimney should have a larger flue.
Typical flue area is 1/10th the fireplace opening area for chimneys 20’ or taller.
Proper operation will depend on an adequate flow of air into the building to replace that which is exhausted through the flue.
Combustible material should be kept at least 2 inches away from the chimney wall. One inche if chimney is completely outside of house wall.
Chimney should extend at least 2’ above any roof ridge that is within 10’
In the best construction the chimney cap should overhang the chimney about an inch. This will allow water to drip off the cap and not run down the walls of the chimney.
Code Requirements for Fireplaces
- Footing min. 12” thick and 6” beyond all sides.
- Hearth min. 4” thick.
- Hearth extension min. 2” thick.
- No combustible material remaining under hearth or hearth extension.
- If opening is less than 6 sq. ft. min. hearth extension is 16” in front, 8” sides.
- If opening is greater than 6 sq. ft. min. hearth extension 20” in front 12” sides.
- No combustible trim or mantles within 6” of opening.
- Combustible material within 12” of opening is limited to 1/8th inch projection for each inch of clearance from the opening.
- All combustion air from outdoors and intake not higher than firebox. The exterior air intake should be covered by a corrosion resistant 1/4″ mesh.
- Smoke Chamber parged smooth.
- Corbelling shall not leave unit cores exposed to inside of smoke chamber.
- When no lining is provided the minimum thickness of smoke chamber is 8”. With lining min. thickness is 6” including the lining.
- Height of smoke chamber from throat to flue shall not be greater than the width of fireplace opening.
- Seismic straps are required at each floor, ceiling and roof level in seismic design category D1, D2. (The Charleston area is D2)
- Factory built fireplaces must be installed in accordance with their listing. Pay attention to this. For example – Although the code requires that the hearth extension be readily distinguishable from the surrounding floor area; a few models of gas prefabricated units are listed for use without a hearth extension. They may also have different clearance requirements. To know which you have to read the installation instructions.
- Normally a gas valve for a fireplace must be in the same room within 6 feet of an appliance and readily accessible. So normally they are not allowed inside the firebox and must be capped off. The exceptions are for factory made appliances. So, appliance shut off valves within the firebox must be according to the appliance manufacturers instructions.2012 reference- IRC 2420.51
- Factory built fireplaces must be equipped with an exterior combustion air supply unless the room is mechanically ventilated and controlled so that the indoor pressure is neutral or positive.
- Masonry chimneys shall be lined. Minimum wall thickness 4”.
- Firebox minimum distance 20”, Rumford firebox minimum distance 12”.
- Spark arester net free area should be minimum 4x the flue area.
Source- 2006 IRC chapter 10.
Common Deficiencies
- Chimney Cap Defects- include missing, cracked or rusted cap which can allow moisture intrusion into the chimney causing damage. Also missing spark arrestor cap.
- Needs Cleaning- Heavy creosote deposits can create a chimney fire.
- Abandoned chimney ports- Sometimes ports are covered over with sheetrock or a pie plate cover which may allow leakage of flue gasses.
- Damaged, Blocked, Deteriorated chimney flues or missing dampers. Rusted through dampers are not uncommon.
- Dead End Flues- This is when a flue vent from another appliance enters an abandoned fireplace at the bottom. These types of flues can easily be clogged with debris. A small appliance flue may not be able to develop a proper draft in a larger chimney causing unsafe flue gasses to spill backwards. Acid produced by the gas appliance exhaust is corrosive to masonry chimneys which will deteriorate them.
- Unlined chimney flue in a single wythe brick chimney- A fire and flue gas leakage hazard.
- Rust and corrosion- Moisture intrusion can cause dampers to rust through and the tops of metal prefab fireplaces to rust through.
- Unsafe clearances to combustibles.
- No cricket on backside of chimney over 30” wide or not flashed correctly- A cricket is a type of rain diverter that diverts rain to either side of chimney. A missing cricket can allow moisture intrusion and damage.
- Cracked or missing refractory panels in pre-fabricated fireplaces.
- On older homes failing mortar both inside the firebox and outside is a concern. Failing (soft) mortar inside the firebox is common in older homes and can be repaired by a professional (special mortar is used).
Now let’s take a look at what we find out in the field.
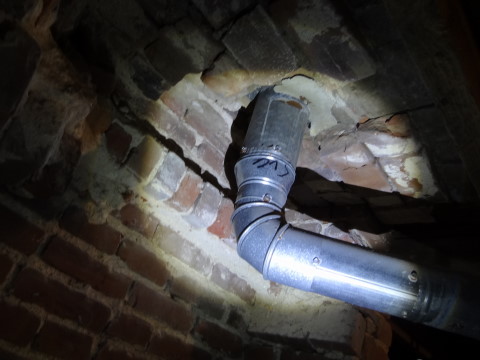
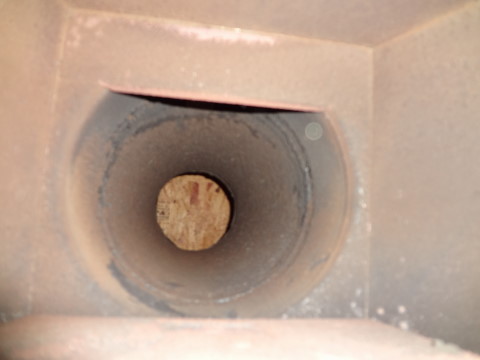
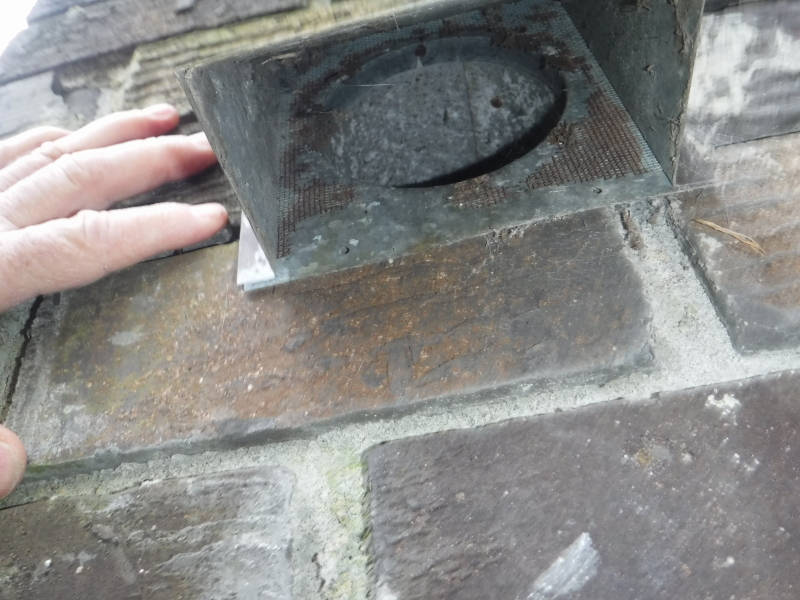
There’s really no end to the scary inspection photos I could show. So I’ll end this here. This article was originally written on my old website on 4-0-13 by yours truly.